热喷涂技术作为表面工程领域的核心工艺,广泛应用于航空航天、机械制造等领域。然而,涂层气孔与裂纹问题一直是行业痛点,据中国表面工程协会数据显示,约 35% 的热喷涂工件因这类缺陷需返工处理。近日,记者走访多家喷涂企业与科研机构,探寻缺陷背后的技术成因。
在某汽车零部件喷涂车间,技术人员展示了未熔颗粒导致的气孔案例:“使用粒度 < 20μm 的铝粉时,氧化率高达 15%,涂层孔隙率超标 2 倍。”
在航空发动机叶片喷涂现场,工程师演示了喷涂距离对裂纹的影响:距离从 100mm 增至 150mm 时,氧化锆涂层表面出现网状微裂纹。
在开放式喷涂车间,检测发现压缩空气含油率超标(0.8mg/m³ vs 标准 0.1mg/m³),导致铝合金涂层出现 “鼓泡” 缺陷。
在南方梅雨季,某企业喷涂的碳钢工件因基材返锈,涂层结合界面出现 “氧化夹层”,72 小时内即产生裂纹。
某海洋工程装备喷涂案例中,钢基材(α=12×10⁻⁶/℃)与 Al₂O₃涂层(α=8×10⁻⁶/℃)因热膨胀系数差异,冷却后界面应力达 80MPa,远超涂层结合强度(50MPa)。
实验表明,陶瓷涂层厚度超过 0.5mm 时,裂纹发生率呈指数增长。某风电轴承喷涂案例中,碳化钨涂层厚度从 0.3mm 增至 0.6mm,裂纹密度从 0.2 条 /cm² 升至 1.5 条 /cm²。
头部企业引入 AI 视觉检测系统,通过高速摄像机(2000fps)实时分析粒子飞行状态,当未熔颗粒占比超过 5% 时自动报警,缺陷检出率达 98%。
中国机械工程学会正牵头修订《
热喷涂涂层缺陷分类及评级》国家标准,拟将气孔率≤2%、裂纹长度≤0.5mm 作为一级品门槛,推动行业质量提升。
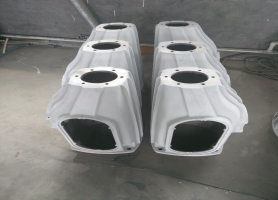